As we have learned from our posts about aluminum sulfate so far, alum is a chemical compound mainly used as a coagulating agent in the purification of drinking water and wastewater treatment plants, among several other applications. This has all been related to the final product, alum. But wouldn’t it be interesting to learn how alum is manufactured? There are several techniques used to create this chemical so let’s dive right in.
In the Laboratory
Alum can be created through one of several chemical processes. One is by adding aluminum hydroxide Al(OH)3 to sulfuric acid H2SO4. The chemical reaction is:
2 Al(OH)3 + 3 H2SO4 → Al2(SO4)3 + 6H2O
Translated to plain english, adding 2 molecules of aluminum hydroxide to 3 molecules of sulfuric acid results in 1 molecule of aluminum sulfate and 6 molecules of water.
Another option is heating aluminum metal in a sulfuric acid solution:
2 Al + 3 H2SO4 → Al2(SO4)3 + 3 H2↑
2 molecules of aluminum metal added to 3 molecules of sulfuric acid results in 1 molecule of aluminum sulfate and 3 molecules of hydrogen gas. (1)
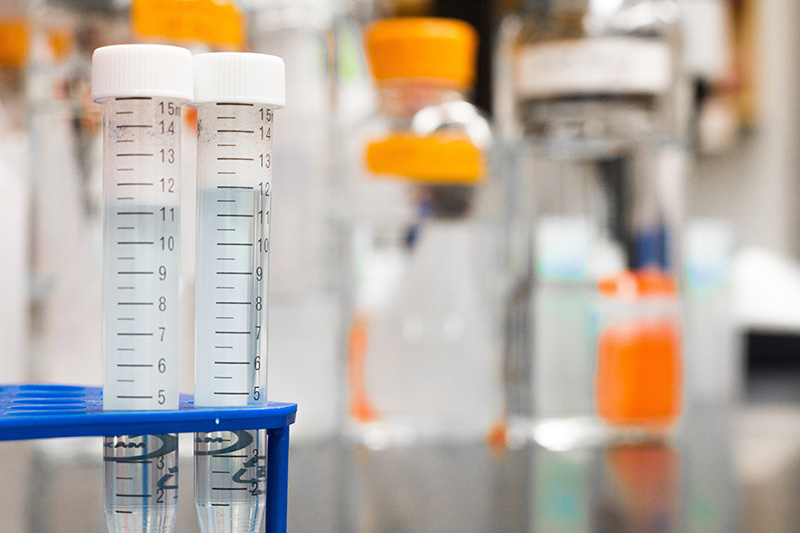
From Alum Schist
Alum schist, also known as alum slate or alum shale, an argillaceous sedimentary rock, often a variety of black shale, containing pyrite or marcasite. Decomposition of pyrite and marcasite by weathering forms sulfuric acid which reacts with aluminous minerals in the rock to form alum and other aluminum sulfates (2).
The schists are either roasted or exposed to the weathering action of the air. In the roasting process, sulfuric acid is formed and acts on the clay to form aluminium sulfate, a similar condition of affairs being produced during weathering. The mass is now systematically extracted with water, and a solution of aluminium sulfate of specific gravity 1.16 is prepared. This solution is allowed to stand for some time (so that any calcium sulfate and basic ferric sulfate may separate), and is then evaporated until ferrous sulfate crystallizes on cooling. It is then drawn off and evaporated until it attains a specific gravity of 1.40. Then it stands for some time, and decanted from any sediment. (1)
From Bauxite
This manufacturing process is the most commonly used as bauxite is a ubiquitous material. It involves reacting liquid sulfuric acid with either bauxite ore containing aluminum hydroxide (Al(OH)3) and hydrated aluminum (Al2O3 ∙ 3H2O), or synthetic hydrated aluminum previously refined from bauxite. Bauxite ore is the main source of aluminum for the world and contains various aluminum minerals and two iron minerals). The process creates hydrated aluminum sulfate per the following reactions:
From bauxite: 3 H2SO4 + 2 Al(OH)3 + 8 H2O → Al2(SO4)3 ∙ 14 H2O
Adding 3 molecules of sulfuric acid to 2 molecules of aluminum hydroxide and 8 molecules of water results in 1 molecule of aluminum sulfate and 14 molecules of water.
From hydrated aluminum: 3 H2SO4 + Al2O3 ∙3H2O + 8 H2O → Al2(SO4)3 ∙ 14 H2O
Adding 3 molecules of sulfuric acid to 1 molecule of hydrated aluminum and 8 molecules of water results in 1 molecule of aluminum sulfate and 14 molecules of water. (3)
From Cryolite
When cryolite is used as the ore for producing alum, it is mixed with calcium carbonate and heated. By this means, sodium aluminate is formed; it is then extracted with water and precipitated either by sodium bicarbonate or by passing a current of carbon dioxide through the solution. The precipitate is then dissolved in sulfuric acid.
The Affinity Chemical Process for Alum Manufacturing
At Affinity Chemical, our process is based on aluminum trihydrate powder. Trihydrate is mixed with water in a batch reactor and continuously stirred or “cooked” for nine hours. The steam that is generated is processed through a scrubber and the batch is allowed to sit for 12 hours, then tested to ensure product specifications are met. A single batch contains approximately 20,000 gallons of liquid alum, enough for five truck loads.
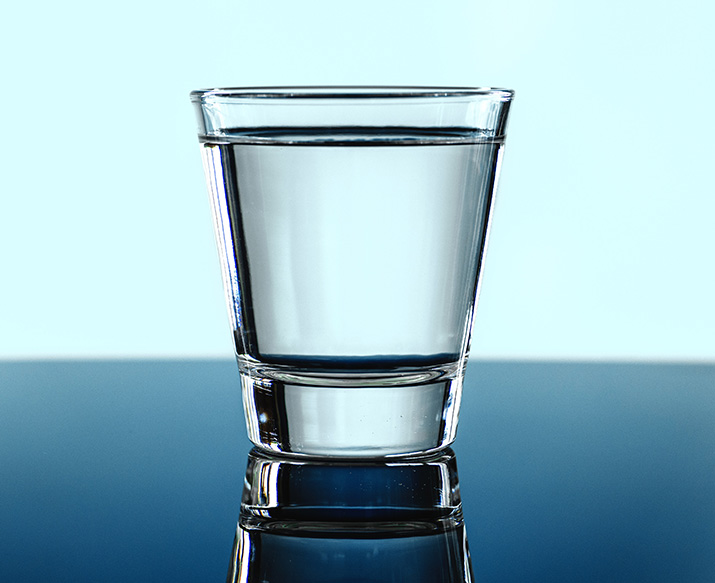
Environmental Benefits
We take great care about the environmental factors related to the alum manufacturing process. Our process emits only steam as a byproduct, compared to other processes which produce additional waste products.
Moreover, we recycle excess alum from one batch and adding it to the next batch, reducing waste and keeping raw material costs low. Every batch is filtered then tested to ensure on-spec product.
Economic Benefits
Our efficient process also enables us to keep prices low. We source aluminum trihydrate from among several carefully-screened suppliers, based on economics and availability. Our focus is always on keeping our prices competitive and our relationships with our customers and suppliers strong.
Dissatisfied with Your Current Alum Supplier?
Interested in purchasing alum from a company who uses environmentally safe methods and cares about their customers? Contact us today!
Resources